The Safe Shop From The Natural Stone Institute
Staying Safe Against Silicosis
Safety regulators are casting a keen eye on air quality. So should you.
What is the problem? All the processes used in the stone industry to change granite into a finished product produce small particles. There is a health hazard when these particles are small enough to inhale.
Our bodies protect us against some dust. Not all the dust that we breathe in gets into our lungs. The larger particles are filtered out in our nose and the tubes leading to our lungs.
Silicosis is a lung disease caused by breathing in tiny particles of silica, a mineral that is part of sand, rock, and mineral ores such as quartz. Only the finest dust particles reach our lungs.
These fine dust particles, which can enter deep into the lungs, are called 'respirable dust'. Usually these dusts are too fine for us to see. Silicosis is irreversible – the particles cause permanent scarring in the lungs, which can harm your ability to breathe.
The natural-stone industry and its vendors have made great strides in efforts to reduce exposure to unseen crystalline silica dust, but there is still a long way to go. One of the best methods to reduce the silica dust is through wet cutting and grinding.
From the OSHA Files
The federal Occupational Safety and Health Administration investigated a stone fabrication shop regarding complaints of unhealthy and unsafe working conditions. Upon entering the shop, investigators observed dust-filled air. No employees were wearing respiratory protection. Investigators sampled air quality and found it to exceed recommended Permissible Exposure Limits (PEL). Information about dust controls or hazardous material was not available to employees. OSHA cited the employer under Section 5(a)(1) of the Occupational Safety and Health Act of 1970, notin that the employer didn't furnish employment, or a place of employment, free from recognized hazards that were causing or likely to cause death or serious physical harm to employees in that the employer did not institute a medical surveillance program for all employees who were or could be exposed to crystalline silica at or above the Permissible Exposure Limits (PEL).
Workers were exposed to respirable silica dust without the protection of an effective medical monitoring program to protect them against the early onset of silicosis.
OSHA issued citations and assessed fines in excess of $4,000 for several serious violations, including:
- The employer failing to administer a continuing, effective hearing conservation program.
- The employer failing to develop or implement a written respiratory protection program with required worksite-specific procedures and elements for required respirator use.
- The employer failing to develop, implement, and maintain a written hazard communication program.
This case was selected as being representative of injuries caused by improper work practices. No special emphasis or priority is implied nor is the case necessarily a recent occurrence. The legal aspects of the incident have been resolved, and the case is now closed.
In shops that are dry or partially wet, or where only sections of the facility are covered with dust-collection systems, these precautions should be taken to minimize exposure to crystalline silica:
For Employers:
- Test your employees to assess your risk: State OSHA on-site consultation divisions can provide free testing. Regular monitoring is a requirement for OSHA compliance.
- Train your employees on the risks of airborne silica. Documented training is a requirement for OSHA compliance.
- It cannot be said too often, or with too much emphasis: Protecting the workplace and employees from respirable crystalline silica – and eventually silicosis – should be one of the most-important objectives of every company in the natural-stone industry.
For Employees:
- Be aware of the hazards of inhaling silica dust.
- Use wet vacuums or water to clean up dust—never use brooms or compressed air.
- Wear washable or disposable work clothes.
- Do not eat, drink, smoke, or apply topicals such as creams or cosmetics after silica exposure until you have washed your face and hands.
- Always shower, if possible, and change to street clothes before leaving the work area.
- Park cars where they will not be contaminated with silica and other substances.
- Wear a respirator when other engineering controls cannot reduce exposures within acceptable levels.
- Limit your exposure to the workplace. When you take silica dust home, you contaminate your house and your car. You will be exposing your family to crystalline silica dust as well.
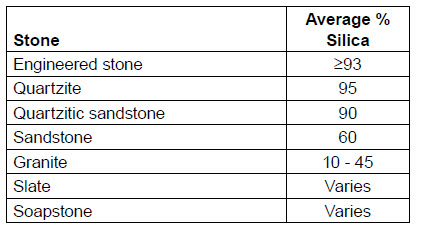
Sources: Silica Hazards from Engineered Stone Countertops, NIOSH Science Blog, March 2014; ASTM C616, Standard Specification for Quartz-Based Dimension Stone; American Geological Institute, Dictionary of Geological Terms
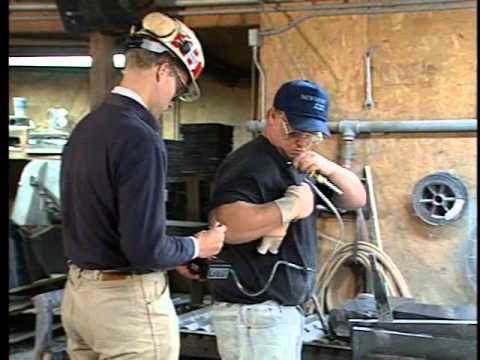
Among the service that hard-surface-fabrication employers need to provide is on-site testing of employees. Regular air-quality monitoring is a requirement under OSHA. (Photo courtesy Natural Stone Institute)
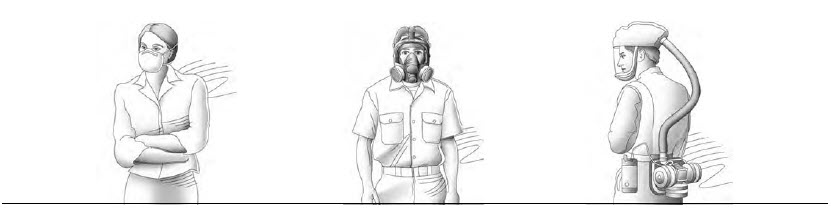
There's a N95 NIOSH-certified respirator for just about any workplace and worker, from a faceplate respirartor (left), a full faceplate elastomeric respirator (center) and a loose-fitting powered air-purifying respirator, or PAPR (right). (Images courtesy OSHA)
Recommendations
The following procedures will minimize the potential hazards associated with hazardous communications in the workplace:
- Provide engineering controls where feasible, such as local exhaust ventilation and/or wet grinding and cutting.
- Provide administrative controls by limiting the amount of time that a worker performs a silica-related work task.
- Wear only a N95 NIOSH-certified respirator, if respirator protection is required. Don’t alter the respirator.
- Provide training, exposure monitoring, and health screening and surveillance programs to monitor any adverse health effects caused by crystalline silica exposures.
(Note:These are only a requirement if exposure levels are above the “action level” or if respirator use is required by the employer.)
Make sure employees are up to date on safety training. All Natural Stone Institute Safety Resources and Courses are offered free at www.uofstone.com and www.naturalstoneinstitute.org/safety/.
The information herein is provided by the Natural Stone Institute as a general summary for use in job site toolbox talks and is provided to augment and not substitute for or replace required training under any applicable local, state or federal workplace statute, law or regulation. It is the user’s responsibility to ensure this content is consistent with job site requirements and applicable statutes, laws or regulations prior to use and make any required additions or changes.