Measuring Up
Pre-set your tools to do all the work.
Previous page: Trend Group production line, Sebring, Fla. Above: Photo courtesy Terminator Diamond Products
By K. Schipper
Everybody likes the idea of getting more production out of their CNC machines … and there’s a fairly simple method to help make it happen. Tool presetters are still more likely to be found these days in metal fabrication and plastic molding facilities, but they’re beginning to show up in stone fabrication shops. And, with good reason. Although manufacturers disagree on how frequently their machines need to be used, they concur that a presetter can help CNC routers produce jobs that need little or no hand-finishing while extending the life of tooling.
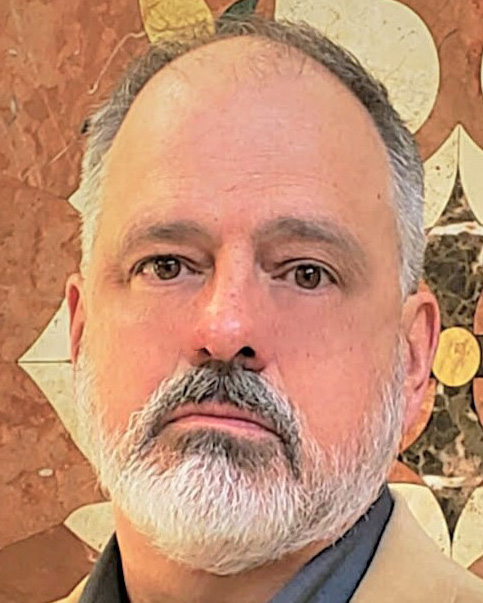
“We’ve seen our users increase the life of their polishers – not the metals, but the polishers – two or threefold.”
Rick Self Terminator Diamond Products
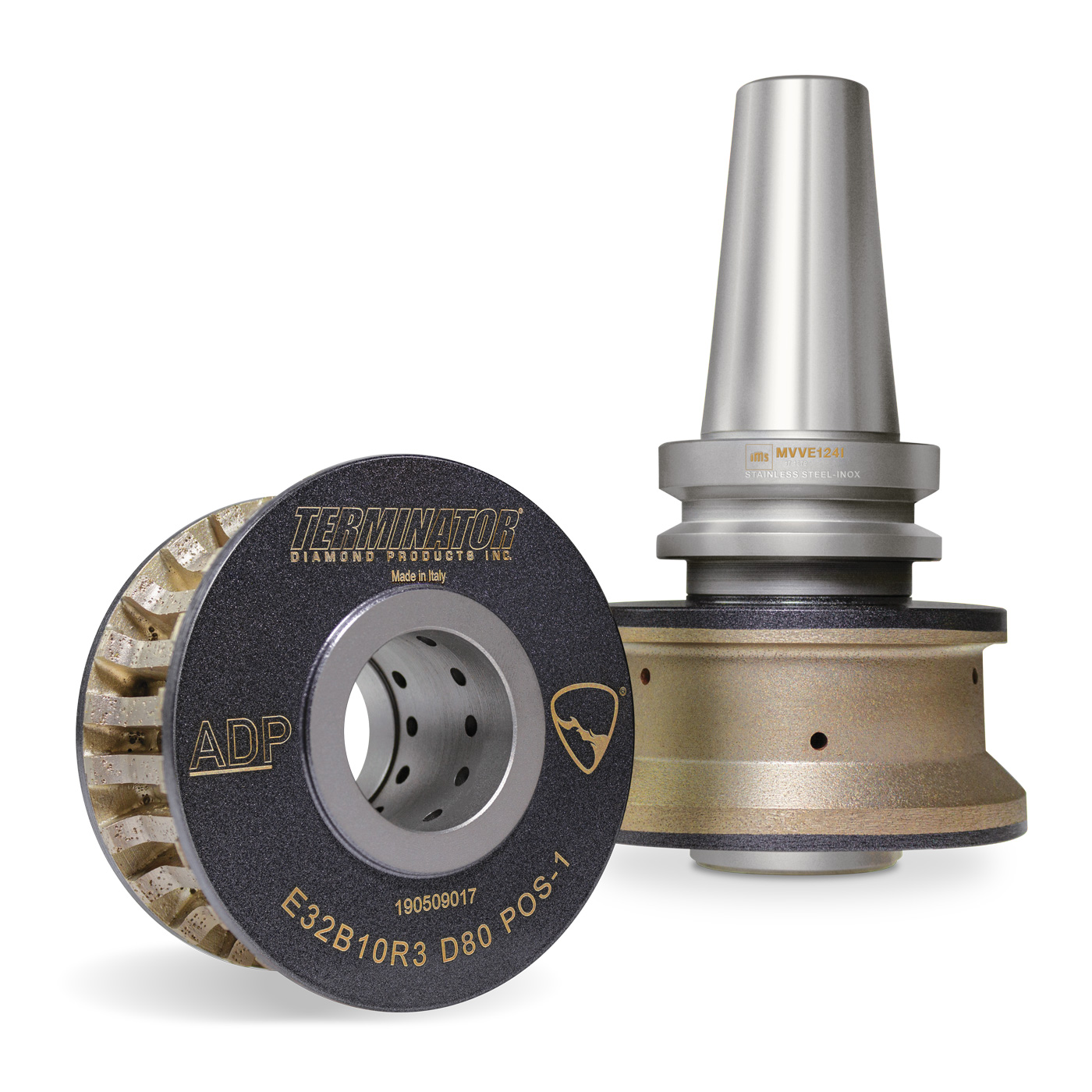
What You Don't Know ....
Admittedly, many shop owners may not even know they’d benefit from having a tool presetter. One representative of a company that manufactures tool presetters uses the word “agnostic” to describe the router manufacturers’ attitudes toward the devices. However, he believes that is changing, an opinion shared by Michael Downey, director of the CNC program at Tucker, Ga.-based GranQuartz. “Now when we start going to shows you’ll find most of the manufacturers have started to embrace the technology and are putting presetters next to their routers,” says Downey. “In the last three- or four-years technology has completely changed where shops have decided to go digital, and this is just one more step towards becoming more efficient.” Simon Bradbury of Dover, Del.-based Stone Industry Group, says it’s a good question to ask because presetting is an integral part of tooling. However, he adds that most CNC users don’t calibrate their tooling because they don’t know how. “The machines have the capability to give a high-gloss finish, at speed, if tooling is calibrated and maintained properly,” Bradbury says. “However, you see a lot of shops running to the last metal, then polishing by hand, which kind of defeats the object of paying a quarter-million dollars for a router.” Regardless of the CNC manufacturer, though, these presetters are not to be confused with the laser tool management systems built into some machines. Rick Self, director of business development for San Carlos, Calif.-based Terminator Diamond Products, says there are a couple major differences between the types of systems. Although there are several ways of measuring tooling, state-of-the-art tool presetters utilize automatic 3D optical scanning that both identifies discrepancies in the assembled tool and provides the final grind dimensions. “Presetting does not utilize lasers in any way,” says Ryan Meleg, vice president of global sales for Fairport N.Y.-based Omega TMM. “We use a full vision system that can more quickly and accurately measure the grinding wheels.” A true presetter is also able to do that measuring offline for several CNC machines, adds Michele Capello, commercial manager of the stone division for Charlotte, N.C.-based Diamut America. “A machine that has a built-in laser measures the tools and presets them for that specific CNC machine only,” he says. Not only is it able to do the measuring offline, but a tool presetter is then able to communicate with the various CNC machines in a shop, according to Self. “Really, tool management is software,” Self says. “True tool management is a primary distinguishing factor between presetters. It involves integration with the CNC machines and the collection of data related to both the calibration and the EDM (electrical-discharge machining) intervals of the tooling. “Your typical laser system has a very difficult time living up to all that a good tool management system can do,” he adds.

“You bought your CNC router to make saleable product, not to measure tools.”
Ryan Meleg Omega TMM
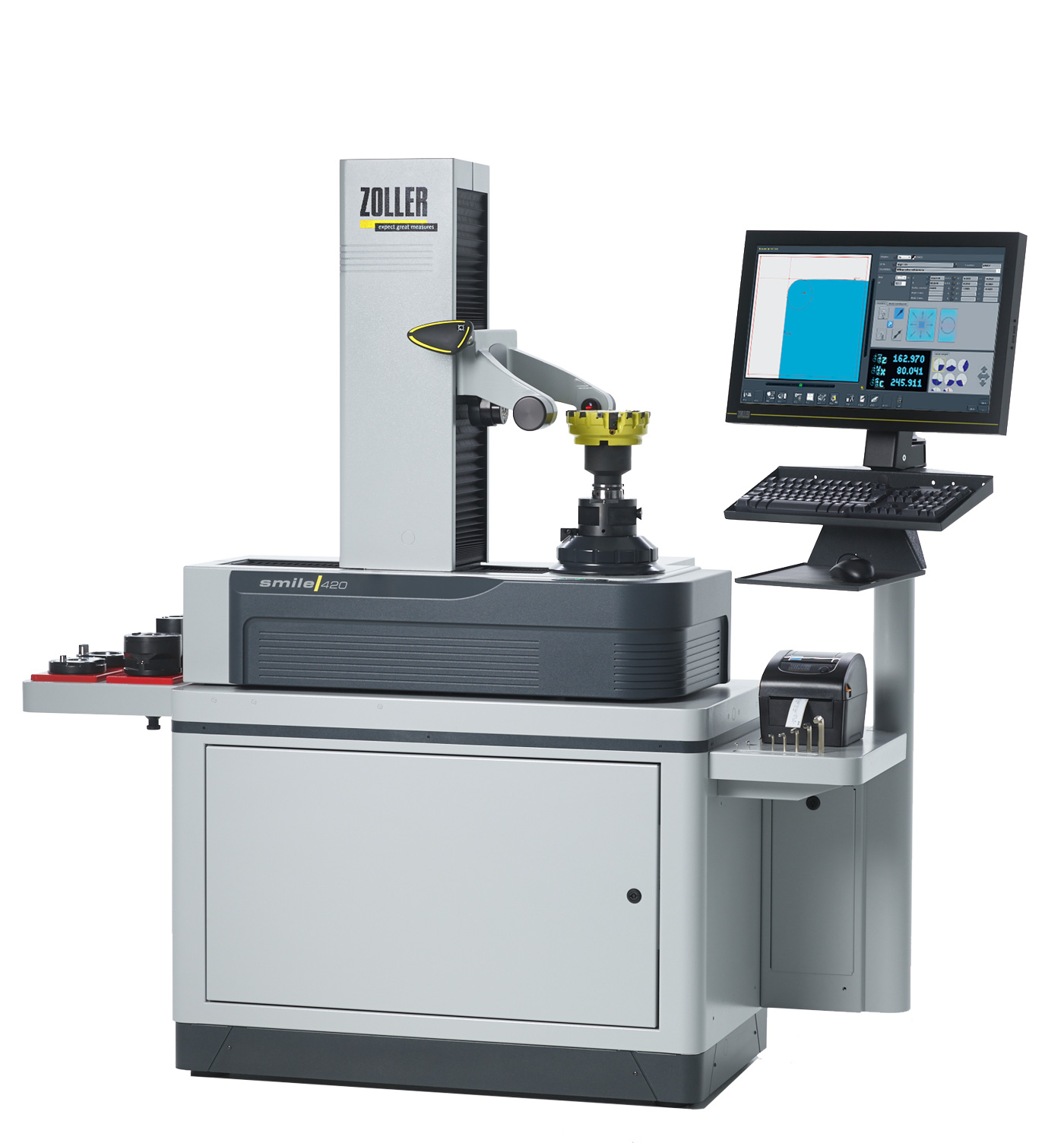
OK, how do these devices work?
Kyle Bush and Ryan Meleg of Omega TMM show how a tool is measured and how the information can adjust a CNC production center to provide optimum use.
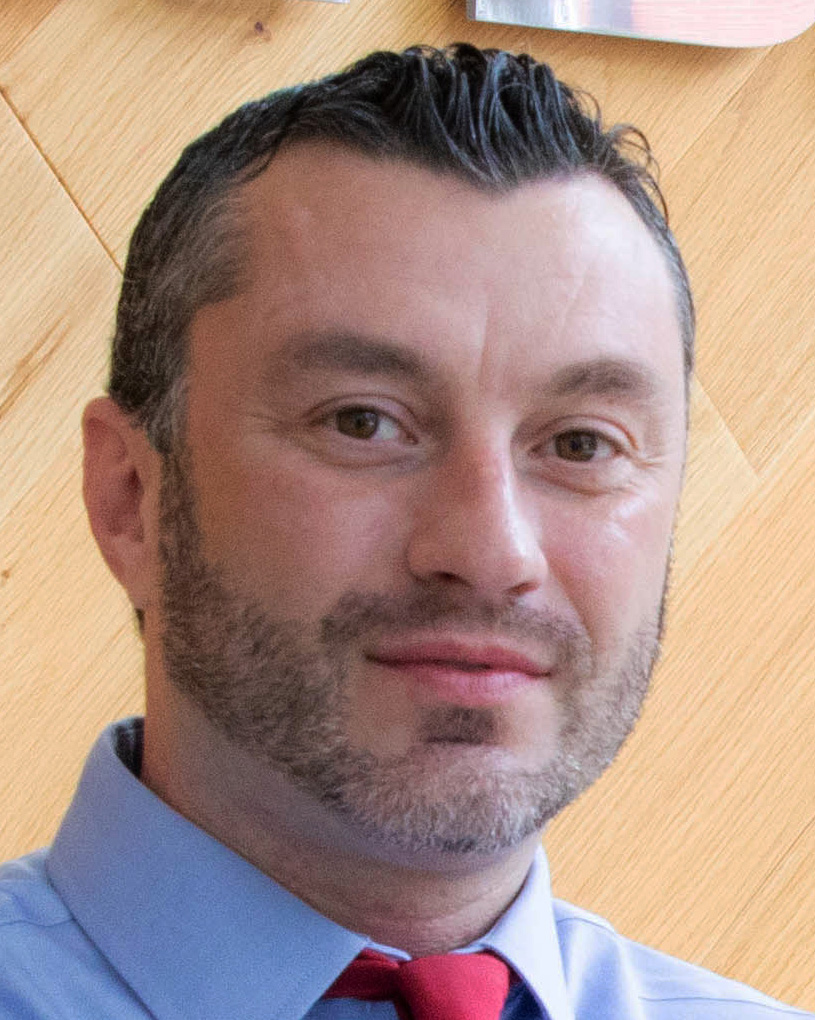
“You get increased efficiency in your manufacturing operations. You get greater accuracy, which translates into a better product.”
Michele Capello Diamut America
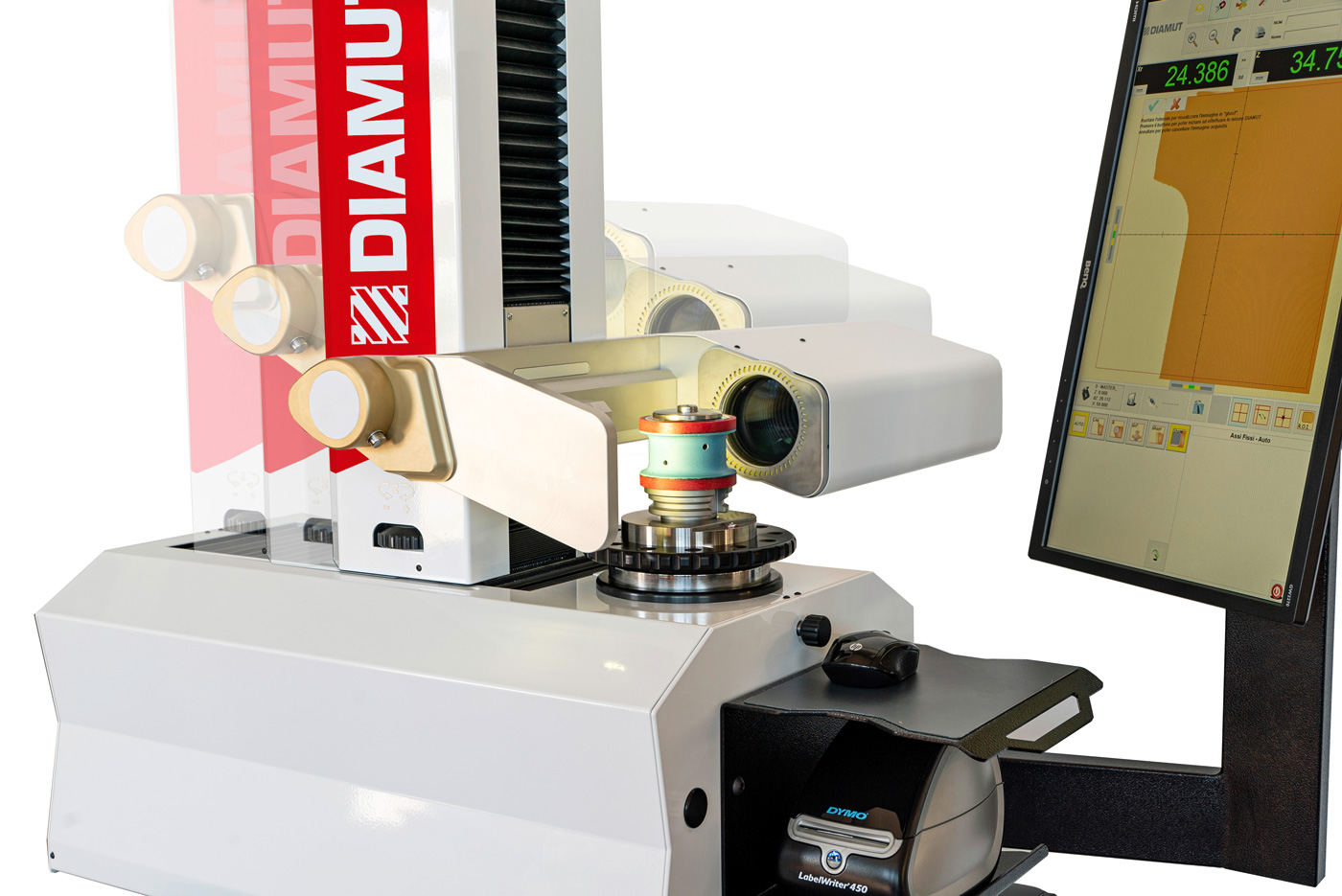
Common Cause
So, just what can a tool presetter do for a shop? Opinions vary slightly, but there are some common themes that run through the responses of these manufacturers. Diamut’s Capello probably sums it up best. “You get increased efficiency in your manufacturing operations,” he says. “You get greater accuracy, which translates into a better product. And a tool presetter is also a great way to optimize the tool life.” For Turrini’s Bradbury, increased efficiency comes because the presetter gives the operator confidence in programming and running the machine. He adds that all tools will benefit, not just a few. “It doesn’t matter whether you’re running flat or complicated profiles,” Bradbury says. “Being able to accurately run all metals and all polishers means no touch-up jobs and that speeds up production and increases margins.” “You can also lower your hand labor if you’re able to take the finished material off the machine and don’t have to pay a guy to stand there and finish it,” agrees GranQuartz’s Downey. “And, when you’re eating the correct amount of grind stock, the polish looks better.” Downey notes that a lot of that is dependent on the quality of the wheel, as well as how it’s cared for and maintained during its lifecycle. Terminator’s Self reinforces Downey’s comments about getting a more-consistent polish when you’re getting better contact between the tool and the stone. “Run-out is caused by either a tool not being centered onto the cone or the tool itself being out of round,” he says. “Or the cone is out of tolerance and causing the assembly to wobble. So, checking for eccentricity of both the tools and the cones is very important.” He adds that shops will likely see the most improvement in their flat and eased edges. The bottom line, says Omega’s Meleg, is that a tool presetter will help a shop save both time and money. “You bought your CNC router to make saleable product, not to measure tools,” Meleg says. “Presetting is done completely offline and can reduce setup time by 90%, which is time and money saved. “There’s also the benefit of increased tooling life and knowing precisely when your wheels need to go out to be EDM’d. You will also see a steep decrease in scrap due to having perfectly measured tools for every job.”
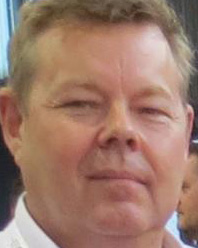
“Being able to accurately run all metals and all polishers means no touch-up jobs and that speeds up production and increases margins.”
Simon Bradbury Stone Industry Group
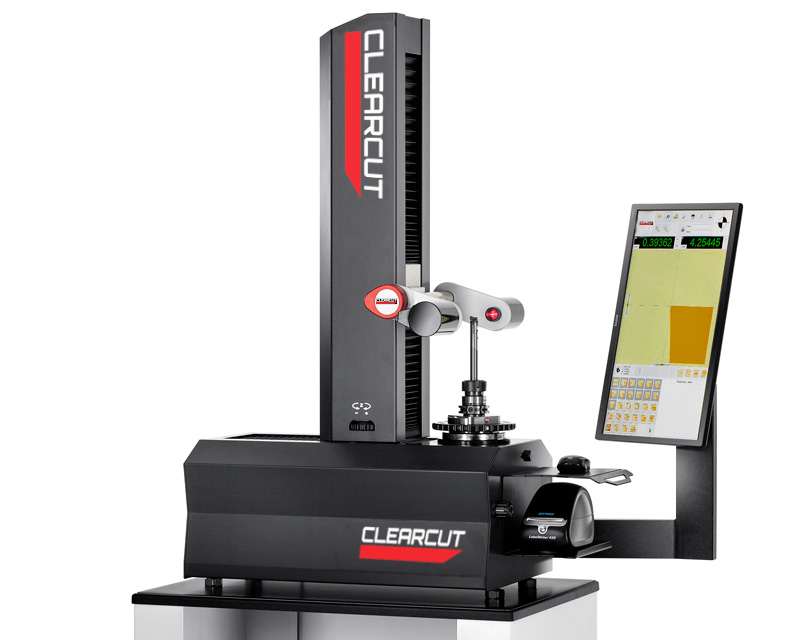
Measuring the Variables
One area where there’s some disagreement between the tool presetter manufacturers is on how frequently tools need to be measured. GranQuartz’s Downey says that company recommends recalibrating a set of tools every 500-750 linear feet of production. “That’s what we’ve found to be the happy sweet spot,” he says. Both Omega’s Meleg and Diamut’s Capello say to maximize production, the presetter should be used before the start of every job. Turrini’s Bradbury suggests a more-nuanced approach, with length being only one factor to consider. “It all depends on the profile,” Bradbury says. “Complicated profiles wear more unevenly and require more attention; flat profiles less so.” Terminator’s Self takes a slightly different look at the whole subject. He says both measuring frequency and recalibration (dressing) are functions of each individual shop. “The measuring intervals will be linked to the construction of the tools, the water provided to the tools and the speed at which the tools run,” he says. “That’s the basic formula for success.” Given the amount of time it takes to measure a set of tools, doing it at frequent intervals isn’t going to be disruptive to a shop’s flow. Five to 10 minutes seems to be the norm. Meleg attributes that to the presetter’s utilization of a full-vision system that can quickly and accurately measure tens of thousands of points on a single wheel in a matter of seconds. “The ability to ‘see’ the actual gives you much greater breadth and depth of measurement capabilities and provides the opportunity to profile the wheels – and to utilize the best-fit metrics,” he says. Nor should training someone in the shop or office to use the presetter be that onerous. Whether that person is the CNC operator depends on the shop’s situation. Or, as GranQuartz’s Downey explains it, “Sometimes it’s the CNC operator, sometimes it’s a guy who oversees CNC operations for the shop. If it’s a shop that has five CNCs, maintaining all the tools can be a full-time job for one person.” The main goal, he adds, is to get repeatable results. Training varies by company and focuses primarily on using proprietary software. It can range from a couple hours that can be done remotely, to three or four days of in-shop instruction. One other caveat: The presetter will likely have to find a home outside the shop environment, although that also varies some by manufacturer. Because these are precision measuring devices, most prefer a cleaner space away from the dust and moisture of the shop floor. However, that’s not always the case. “The presetter performs better in a cleaner environment,” says Diamut’s Capello. “But, you know, we offer protective features, and it can be used next to a CNC machine, especially if it has an enclosed magazine. With little maintenance it can be used in the shop as well.” The return-on-investment with a tool presetter can be substantial, regardless of how you choose to look at it. Capello says it varies by shop, and among the variables are the cost of the machine, the cost of labor, and the increased capacity to produce with a presetter. GranQuartz’s Downey agrees that there are several factors to be considered. One is how much longer tools will last with frequent presetting – which Downey puts at 35% to 40%. Another is how many jobs can be taken off a CNC without requiring hand-finishing. “Typically, we tell people with one machine they’ll see an ROI in six-to-eight months,” Downey says. “With two machines, it’s four or five months. I’ve yet to have anybody say it’s longer than a year.” Terminator’s Self goes back to what a shop isn’t spending on new tooling by using one of its presetters. “We’ve seen our users increase the life of their polishers – not the metals, but the polishers – two or threefold,” he says. “And it increases the life of the metals significantly. That’s 40% to 50% for diamond 1 and between 100% and 200% for diamonds 2, 3, and 4. That’s significant.” Turrini’s Bradbury estimates his system will at least double the life of any tool that’s preset frequently. And he offers this formula for figuring the possible ROI. “Take the annual amount you spend on profile tooling and halve it,” he says. “Then, take the time spent setting up and manually adjusting tools and total that. Now, double it as you gain that production time, too. Add those together and it will typically add up to way more than the cost of our presetter in just one year.”