Under Pressure
Picking the Right Pump for Optimal Waterjet Production
Photo courtesy KMT Waterjet Systems
By K. Schipper
Waterjet cutting systems can run with two different types of pumps -- intensifier and direct drive – and there isn’t necessarily a simple answer as to which one is going to be the better choice in a given situation.
The good news: these systems aren’t as delicate as some people think. Yes, they do require some care and regular maintenance, but unless you’re working the waterjet 24/7, you’ll get plenty of maintenance-free production.

Intensifier pump
(Illustrations courtesy Wardjet Corp.)
A TALE OF TWO PUMPS
Both types of pumps work for fabricating stone, quartz or porcelain. So, why are intensifier pumps more popular, at a ratio of about 80% to 20%?
“The most important difference is the long-term cost of ownership,” says John Branch, vice president of sales for St. Michael, Minn.-based Jet Edge Waterjet Systems. “The direct-drive pump is less expensive to purchase than an intensifier pump.
However, after about 4,000 hours of operation (with direct drive) you will have spent the capital difference in consumable parts on the direct drive pump.”
Why is that? For starters, intensifier pumps have been used in the cutting industry for much longer than direct-drive pumps, says Brian Sherick, vice president of North American sales for Flow Corp. in Kent, Wash.
As a positive-displacement pump, direct-drive pumps are also producing water at full capacity whenever the motor is running. That’s great if a machine is actively cutting; when the head stops, however,vwater will be sent down the drain until cutting resumes.
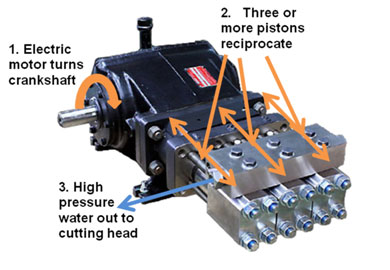
Direct-drive Pump
Both types of pumps mechanically push water at a higher rate. Here's how an intensifier model uses a valve operated with pressure-driven hydraulic oil to accelerate water flow. (Illustration ©Ingersoll-Rand/courtesy KMT Waterjet Systems.
Direct-drive units are typically smaller than an intensifier pump, with many small parts that move very fast, Sherick adds.
“If things go bad, they do so very quickly,” he says.
Not only are the parts small, says Cevin Moberly, national sales director for the stone division of Caledonia, Michigan-based CMS, but the maintenance can be complicated.
“It usually requires the assistance of an outside factory technician to do the work,” he says. “The intensifier pump won’t run quite as long, but typically, the customer can do his own maintenance.”
The trade-off might be worth the additional investment in maintenance if the direct-drive system performed better, but that isn’t the case either. Flow’s Sherick observes that intensifier pumps provide more throughput and faster cutting of thicker materials.
“Plus, intensifiers are available with a wide range of pressures and horsepower levels that can be tailored to a customer’s business,” he says.
In the waterjet industry, the most-common pressures are 60,000-psi and 90,000-psi, with dual capabilities common, although the higher pressure isn’t usually supplied to the stone industry.
“I’ve heard there are even machines that cut at more than 90,000 psi, but we don’t supply them,” Moberly says. “And, since everything is related to everything else, cutting speed and pump performance have more to do with cutting quality than anything else.
"Optimum feeds and speed-per-material gets you the best quality edge; let the cutting media do its work.”
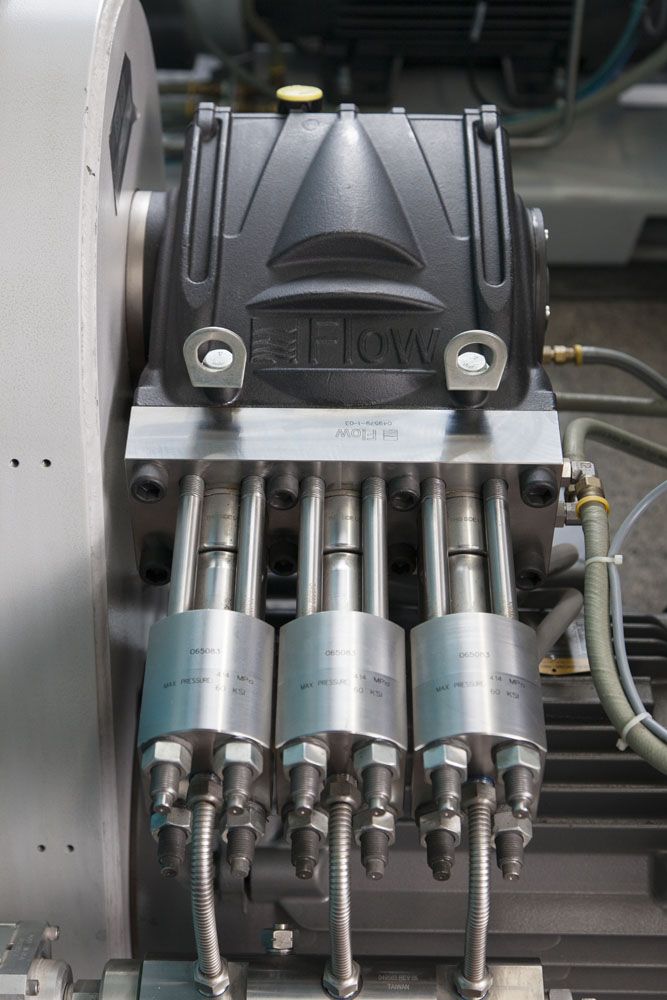
Direct-drive units typically use three reciprocating pistons, such as this Flow model. (Photos courtesy Flow International Corp.)
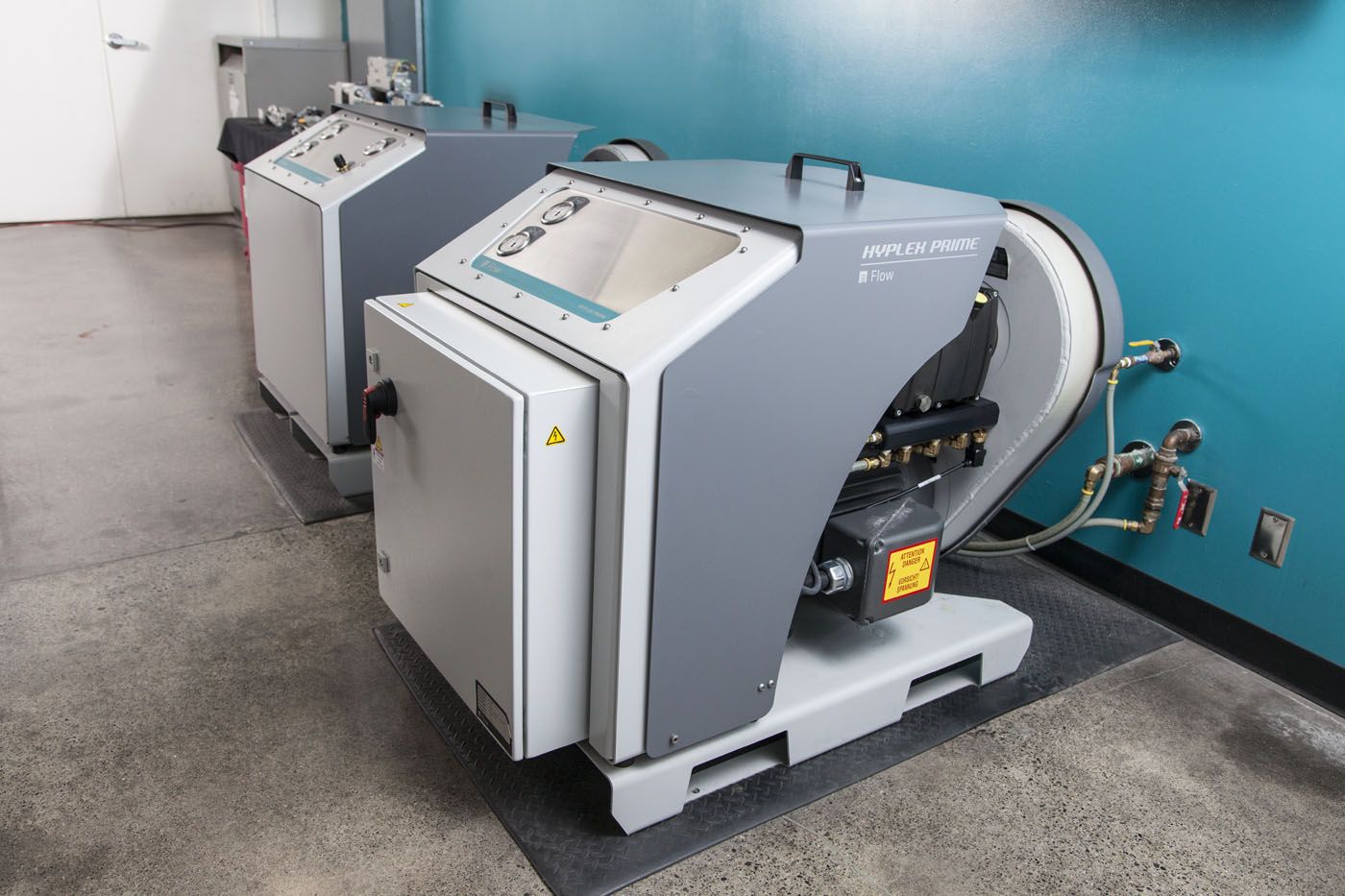
THE CASE FOR BETTER WATER
By media, Moberly’s referring to the garnet cutting material that’s fed into the water stream. Both it, and the size of the orifice through which the water come, do matter. For those common countertop materials – natural stone, quartz and porcelain/sintered slabs -- opinions vary on whether different pressures are necessary.
Jet Edge’s Branch says piercing pressures may be different for most materials, but Bob Pedrazas, marketing manager for Baxter, Kan.-based KMT Waterjet, says using one pressure for stone material cut by a shop isn’t necessarily incorrect.
“We’re doing some testing now at 90,000 psi with the porcelain materials,” he says. “We are waterjet-cutting porcelain to 90,000 psi to determine if you can really cut faster without any kind of fracturing or cracking or breaking.
“Many metal fabricators are upgrading their pumps to cut at 90,000 psi because of the productivity, but it’s not going that way in the stone industry.”
Both Pedrazas and Sherick note that faster cutting at higher pressures can reduce the amount of garnet used, saving money in the process. And, fabricators are well advised to talk with both the manufacturers of their equipment and the suppliers of their substrates about the best cutting speeds/pressures for a specific material.
As for the water stream itself, the water the shop may be using – and reusing – for other purposes likely will not be clean enough for that waterjet pump.
“Water quality is very important as it will affect the life of the seals, so it’s worthwhile to remove as many particles from the water as possible,” says Jet Edge’s Branch. “Most manufacturers will test your water quality and make recommendations based on the results.”
The big issues are total dissolved solids (TDS) and the hardness of the water. Sherick says those can be addressed by prefiltering the water and utilizing a water softener.
“For those concerned with water consumption, closed-loop filtration/cooling options are available,” Sherick says. “These systems filter and cool the water used for cooling the pump, the cutting water, or both.”
Maintaining the water temperature for a waterjet pump is more critical than with other shop equipment, Moberly explains.
“Using overheated water for the input side of the pump can endanger the life of high-pressure parts, which is why some shops have cleaning and cooling systems dedicated to the waterjet,” he says.
Bottom line: The better the water quality, the fewer problems you’re going to have.
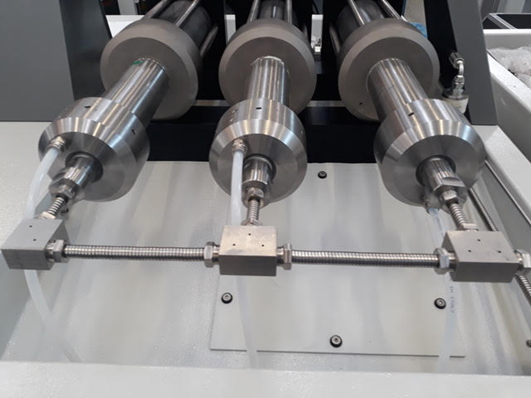
While the designs may differ, intensifier units share the same mechanics. (Photos courtesy CMS [top], Flow International [middle], Jet Edge Waterject Systems [bottom])
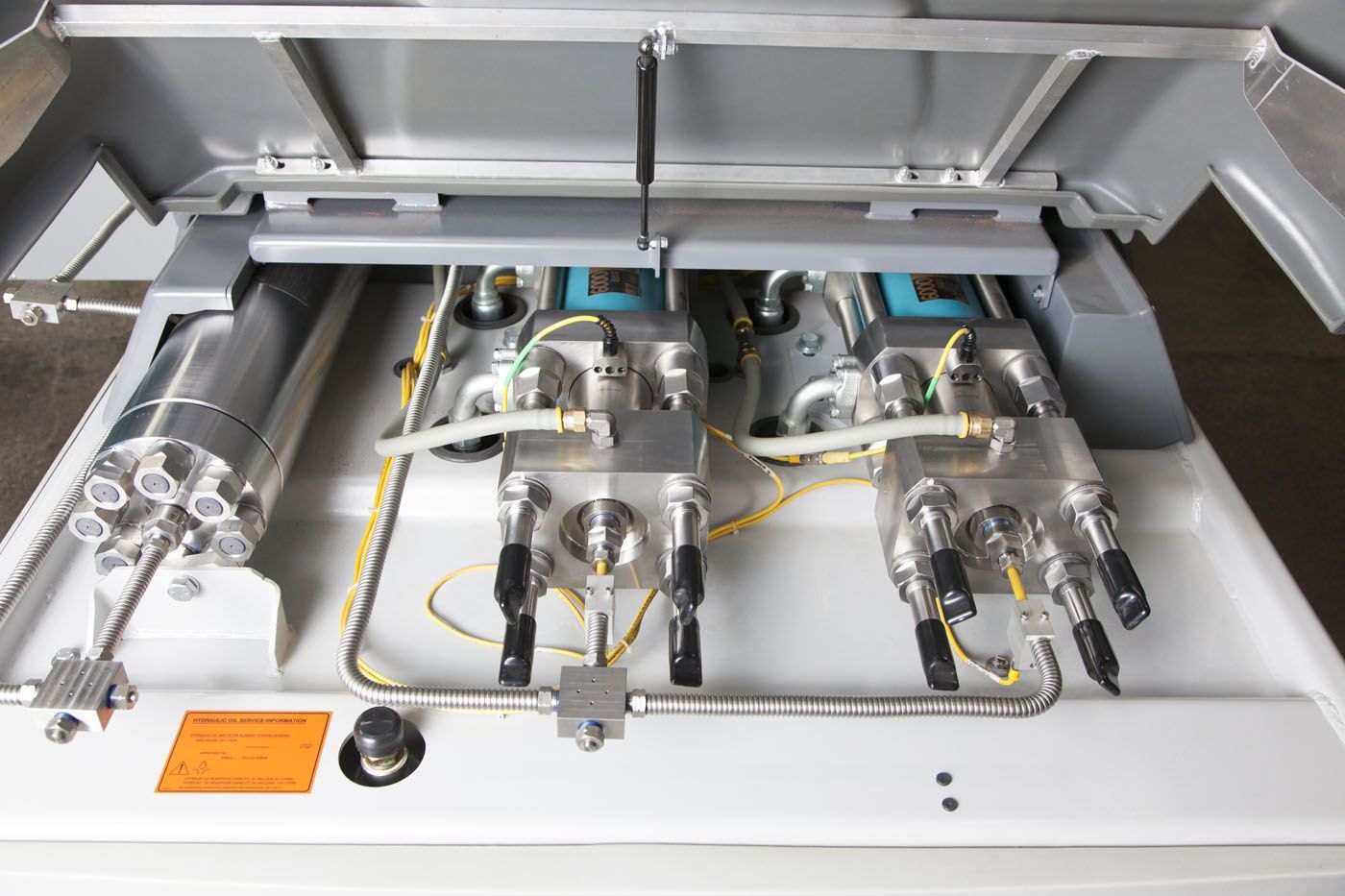
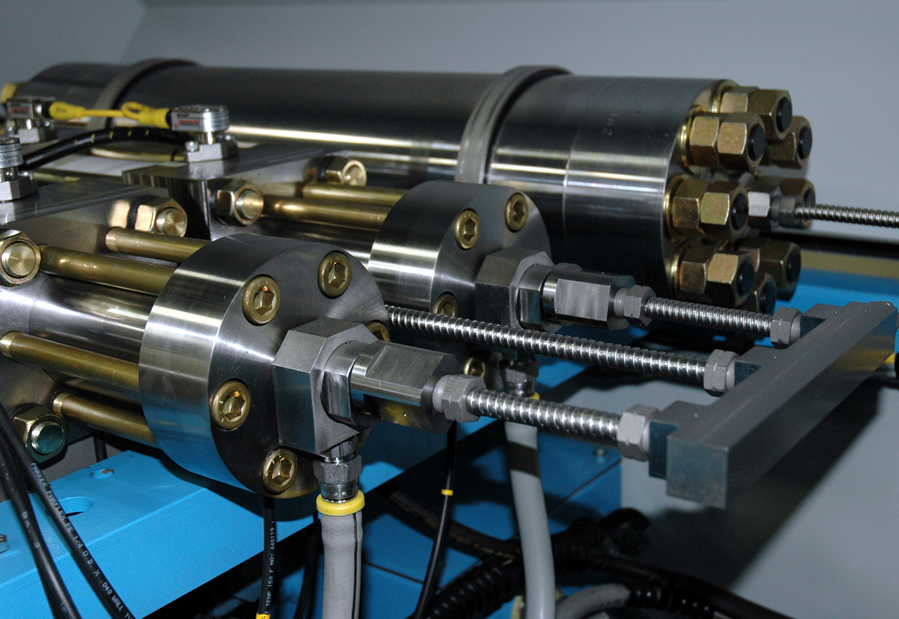

Companies differ on maintenance -- at KMT (top) the emphasis is on factory-representative service. BACA Systems, meanwhile, developed a shipping case (bottom) to ease quick sending of rebuilt parts to be installed by in-shop personnel. (Photos courtesy KMT Waterjet Systems, BACA Systems)
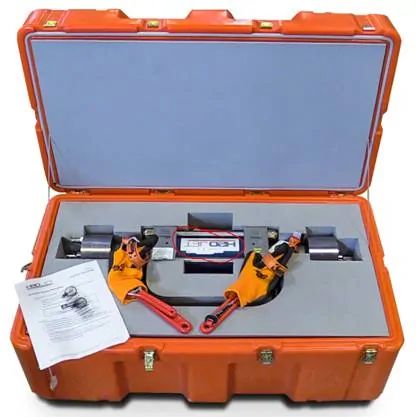
STAYING "LOCKED AND LOADED"
For the shop that may be supplementing its saw with a waterjet – in other words, using it for parts of each day, but not as the primary production device – Flow’s Sherick says water quality and temperature will have the greatest impact on how frequently maintenance is required.
“In the best cases, we’ve seen intervals of more than 1,500 hours in shops with great water quality,” he says. “Typically, for preventative maintenance on filters, a range of 200-1,000 hours is seen.”
Each pump manufacturer handles maintenance a little differently, and there are different opinions on whether even working on an intensifier pump is a do-it-yourself project or should be left to the professionals.
For instance, Jet Edge’s Branch says the most-important maintenance a shop can do is monitor for leaks.
“It’s important to fix it as soon as possible,” he says. “If you wait to repair a leak, it can damage other components that now need to be replaced, costing more in the long run.”
He adds that Jet Edge offers free lifetime maintenance training at its plant for any of its pump users.
Moberly says CMS provides a maintenance schedule with its machines and adds that on-going maintenance of the orifice is a must.
“It’s not hard to change the orifice,” he adds. “They’re relatively inexpensive. Cleanliness of the machine and the water, along with head maintenance, are important.”
KMT’s Pedrazas says that company isn’t as keen on having the guy in the shop do the maintenance. He compares it to taking your new truck to the dealership for service, versus using a neighborhood service center.
“You’re dealing with a very high-precision, high-pressure machine,” he notes. “When it comes to preventive maintenance, we put our seal of approval on it with KMT provides the service, but in the shop that maintenance person is tightening it up based on their strength, but possibly not to specifications.”
He adds that KMT prefers that shops utilize the company’s preventive maintenance program so that shop owners don’t have to worry about things like a minimally trained shop employee doing the maintenance.
Still, the company has some 30 videos on its website explaining every aspect of maintaining its pumps.
Maintenance can be key if you decide to add a waterjet to your shop by buying on the used market, as well.
“A high-pressure system is susceptible to damage if it’s not maintained,” says CMS’s Moberly. “We do sell individual pumps, but I’d be concerned about buying a used machine.”
Both Flow’s Sherick and Jet Edge’s Branch recommended getting the service records and maintenance history from the pump’s OEM before making a purchase and see if a warranty is available.
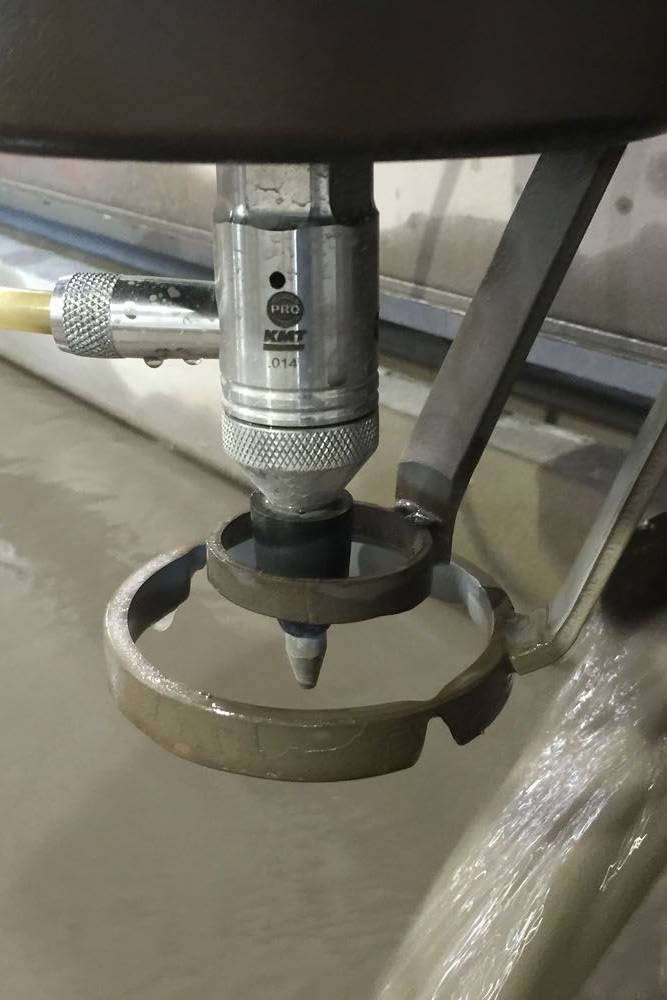
Like other shop tool, good output depends on more the motor or pump. Keeping track of the waterjet's orifice is key to making precise cuts. (Photo courtesy KMT Waterjet Systems)