Espresso & Stone
Travertine Mixes Well in Downtown Toronto
All photos by Riley Snelling / courtesy v2com
By K. Schipper
TORONTO – Just getting natural stone into a container is a supply-chain problem worldwide … but how about installing it? The result is certainly a unique combination here, with a steel-box exoskeleton housing plenty of travertine to add a creamy-and-dreamy air at a downtown coffee shop.
Project: Milky’s Cloud Room, Toronto
Designer/Contractor: Full Fat Studio, Toronto
Stone Supplier/Fabricator: MARBELA, Toronto
Stone Installer: Classic Tile, Brampton, Ont.
Lighting Designer: Anony, Toronto
Many people expand their creative horizons by taking up a hobby. Not Fraser Greenberg. He opted to build and open a coffee shop, and then a second one. While the original Milky’s relied entirely on Greenberg’s background as the co-owner of a hardwood flooring company, Relative Space, for its décor, he says for the second shop he wanted it to be distinctly Milky’s, yet with its own personality. That the shop is in a 585 ft² shipping container might be all the uniqueness some people would need. Instead, he wanted to create what he calls “a dynamically changing interior.” It’s important to realize that the site of the second Milky’s is in a location called stackt market, which opened in April 2019. Besides being the largest container market in Toronto, it’s dedicated to the idea of a lack of permanence. “We liked the idea of shadows of clouds moving over the walls,” Greenberg says. “Clouds are just perfect for that because they move slowly in very inspiring and unpredictable ways. The whole concept was that we have this inside space, but it would be a dynamically changing interior. “The question became, how do we create that sort of effect?” he adds. The answer proved to be twofold. Part of the magic of clouds is having a moving light source. In the case of Milky’s Cloud Room, the greater part of the lighting comes from a custom-designed system of ceiling lights created by Anony and designer Christian Lo, who is also a partner in Milky’s. Greenberg explains that it’s not a typical architectural lighting setup, instead utilizing a system more common to stage events and concerts. “It’s very slow-moving; it’s on a 30-minute loop,” he says. “It takes that long for a light to move from the front to the back. The whole idea is that if you were to stare at the wall, you wouldn’t see any perceptible change, but in the time it takes to place an order, make and get a coffee, that’s when you’ll notice it’s changed.” However, the shop also gets natural light from glass doors on the south and east of the container, as well as reflected light in the evenings from a nearby residential building. “It’s one of those unintentional things that are really nice, because it’s all-natural light that just further emphasizes how attractive this is,” he says. One thing Greenberg knew he didn’t want for the second Milky’s was wood. As he says, the shops are not a franchise. However, he does enjoy design. After turning to an architect/design firm to develop the first Milky’s, the Cloud Room was designed and built by yet another of Greenberg’s career expansions, called Full Fat Studio. Looking for a “not wood,” he began thinking about stone. “Stone became an interesting idea just because of the contrast between the permanence of a stone object versus the temporary nature of a container market,” Greenberg says. “That was our starting point.” To make the idea of stone a reality, he turned to MARBELA, a stone specifier, importer, and fabricator, and Hirad Badizadeh, the company’s president. “That was our starting point,” says Greenberg. “After talking with Hirad we started learning about all the possibilities of what you can do with stone. We started with a whole bunch of samples, and then we saw the one sample of white travertine that we really liked.”
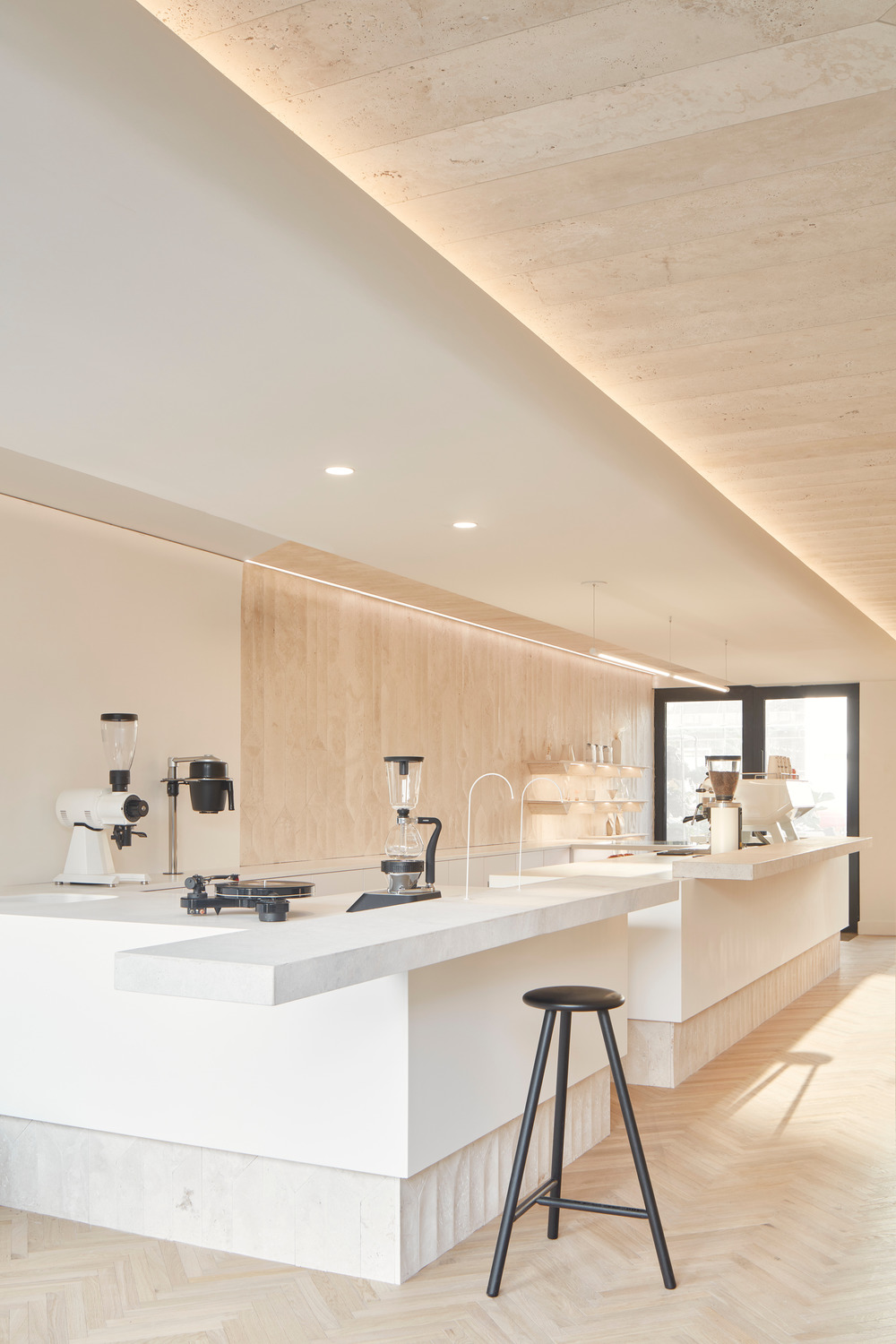
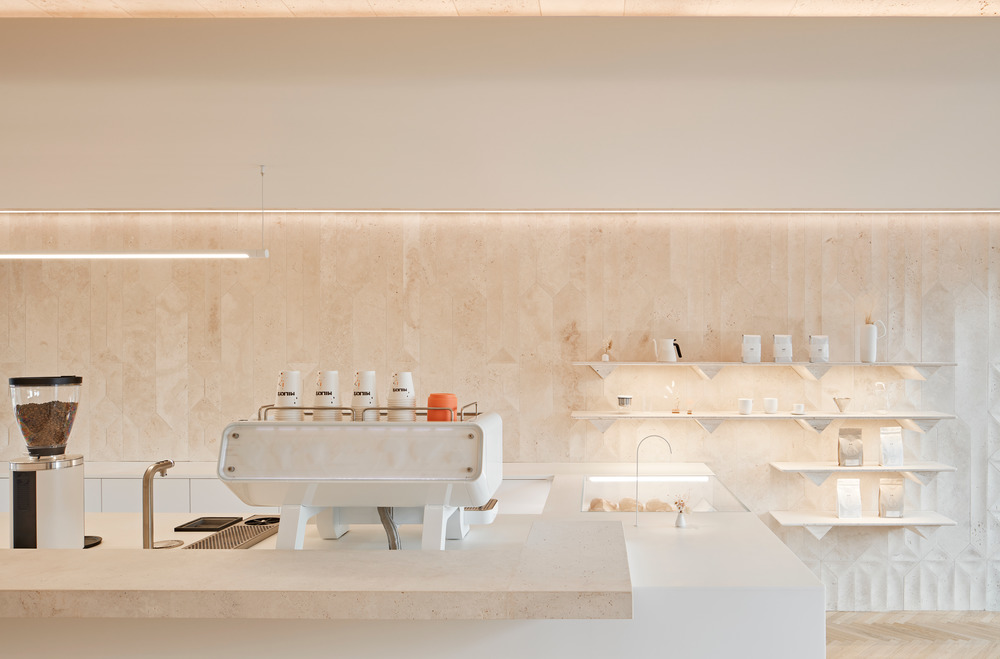

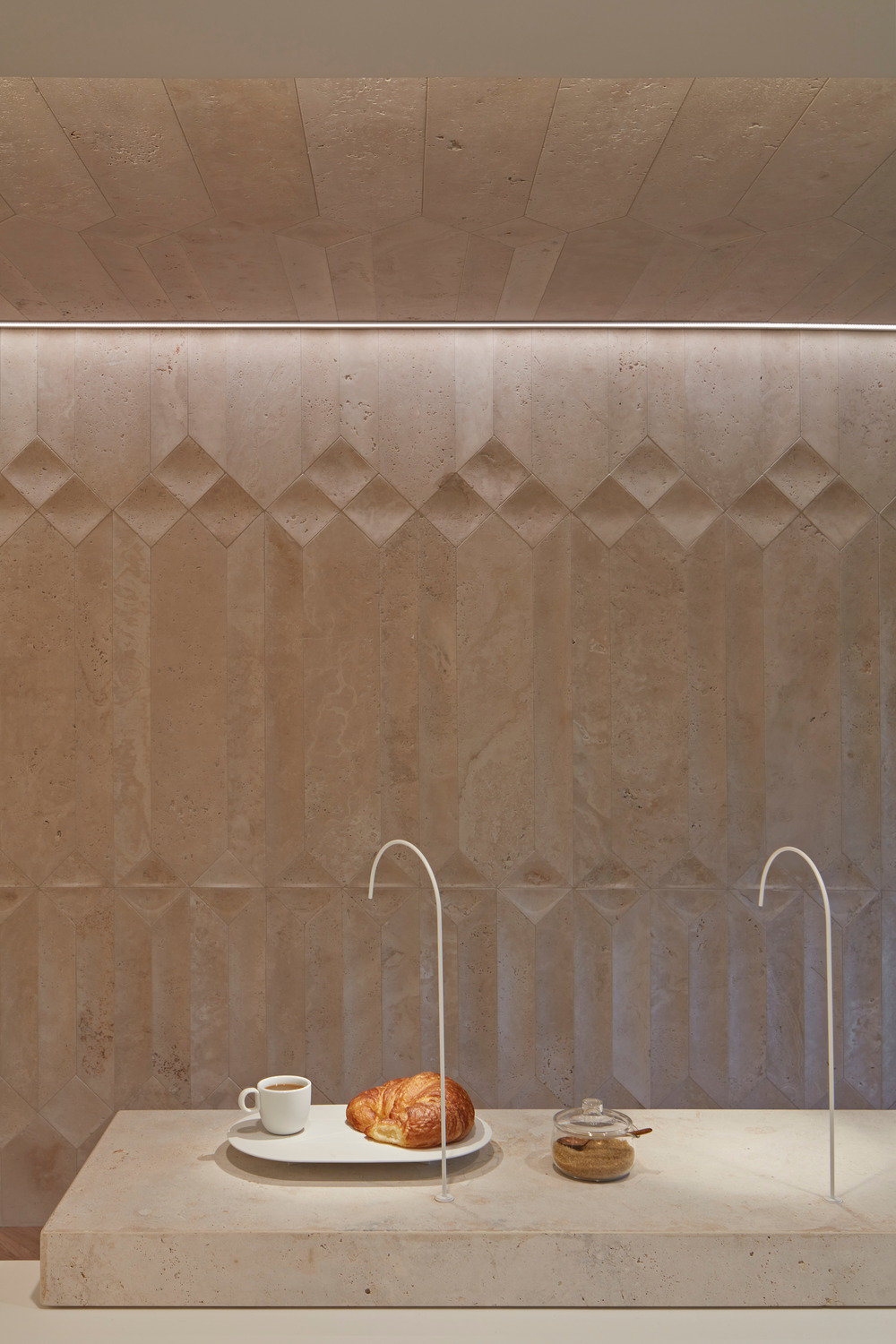

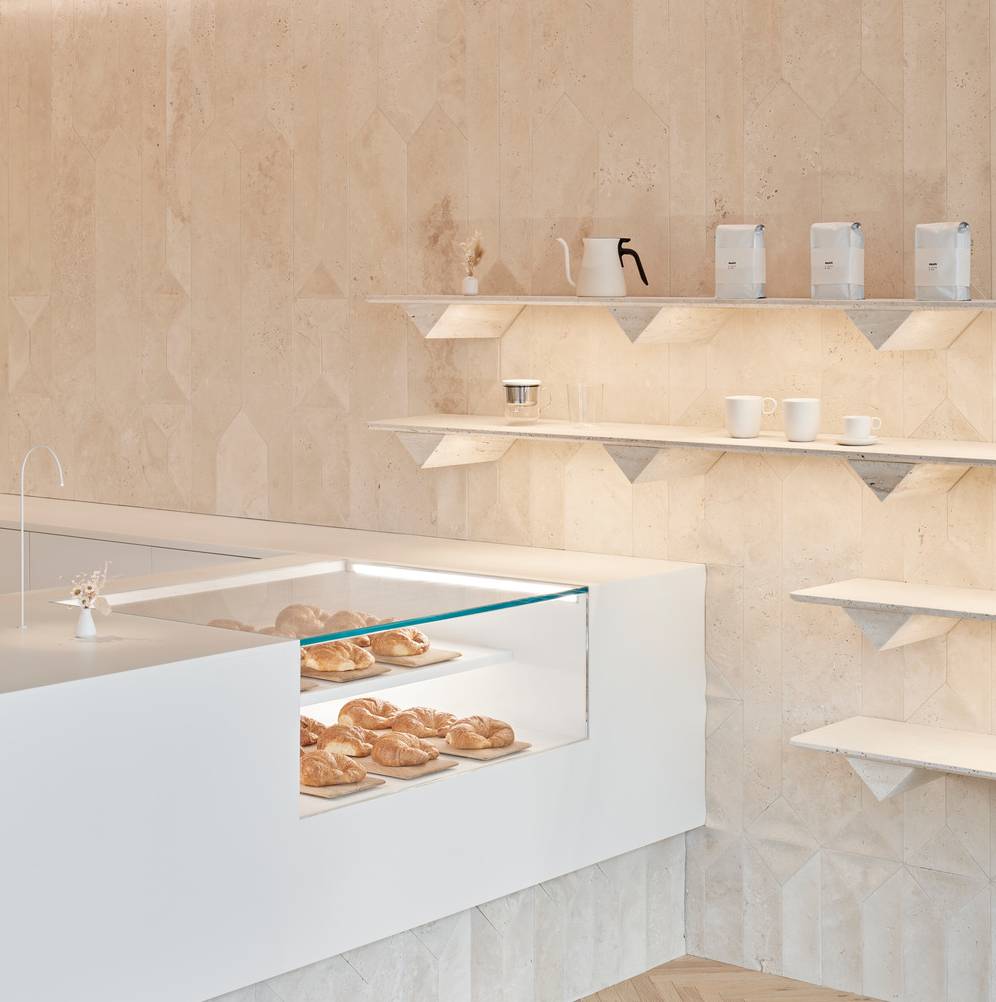
Badizadeh explains that MARBELA collaborates closely with designers from the beginning of a project, helping with the selections of stone colors and patterns, as well as the technology needed to reach the end goal. Although the company didn’t do the final installation, which was handled by Classic Tile, he monitored that process for Greenberg. For this project, Badizadeh says one of the first things he thought about would be the importance of a natural look. That meant no shine, no epoxy, and no fillers. After additional consideration, he proposed a travertine, and one that had been fleury-cut. “By cutting the stone along the grain, we were able to reveal cloudiness and circular patterns within the stone, with some warm color patches,” Badizadeh says. “Going across the grain also gives it that natural organic look that I think is suited for this design.” Ultimately, the decision was made to go with the white Iranian travertine. MARBELA imported the blocks and as with so many other imports this year, simply getting the stone to Toronto proved to be a challenge, as did getting the tiles fabricated in a timely manner. In the end, because of the desire to get most of the construction wrapped up over the summer, Badizadeh says his company had less than a month to get the travertine cut into 17mm-thick tiles and sculpted (at its thinnest it is now 13mm). The tiles are in a variety of shapes with the edges hand-cut and hand-honed for close tolerances. Getting the textures on the surfaces was created by a three-axis, four-spindle CNC router, and the overall designs were planned. Greenberg says the lighting played a significant role in that. “Once we knew the lighting system could achieve the effects we wanted, it helped us know exactly what sort of depth we needed in the stone,” Greenberg says. “It also gave us the ability to do some renderings and see exactly what the effect would be before we went ahead.” And, because the lighting designer is also an industrial designer, it was then easy to create the three-dimensional stone pieces using SolidWorks® 3-D software. Greenberg says there was an intuitive side to the process. “There’s the sense that if the light is here and the object is there, you can get an idea of what will be illuminated,” he says. “But we really wanted this to be a very subtly beautiful space. And we needed to see exactly what it was going to be.” In the end, a total of 850 ft² of travertine was mortared to the walls and ceiling, with another 44 ft² in countertops. Somewhat atypically given the use of stone elsewhere, the floor – a small herringbone pattern – was done in wood by Greenberg’s Relative Space. The shop had a soft opening in October, with takeout only, and Greenberg says he’s enjoyed seeing the reactions of people to the space. “I’m fascinated by how many people walk in and they don’t talk to us to order a drink, but they go to the walls,” he says. “They want to touch it. A lot of people aren’t used to seeing stone look so natural.” Now, Greenberg says he’s interested to see how the stone ages. “You have to design not for Day One, but for Year 10,” he says. “I love thinking about how the space is going to change as it acquires some history.” Certainly, the project has had its impact on Greenberg. He expects there will be another Milky’s in the future, although, “we aren’t thinking of another location yet.” However, the idea of designing space, and utilizing stone has caught his attention. “That’s why we started Full Fat Design,” he says. “We’re working on a bakery now, and we have a couple other projects coming up. And there will be stone on them, if we can convince them to go through the same labor to get this beautiful product.”