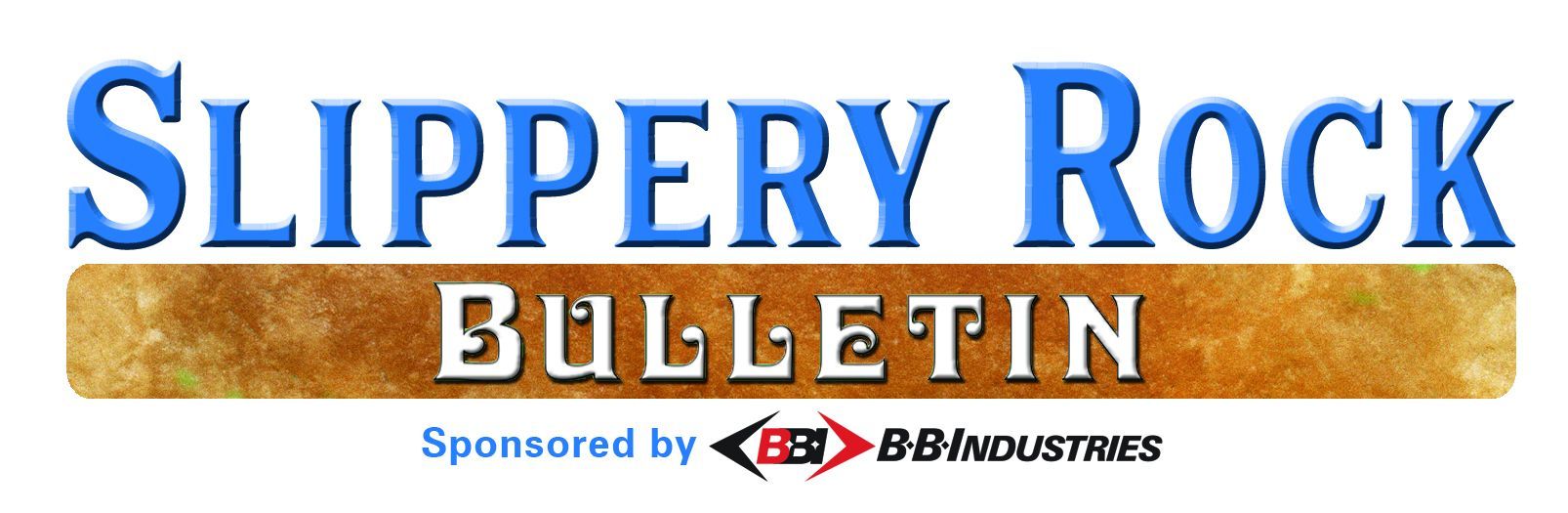
▼ There's More! ▼
From Rock 'n' Roll to Rocks
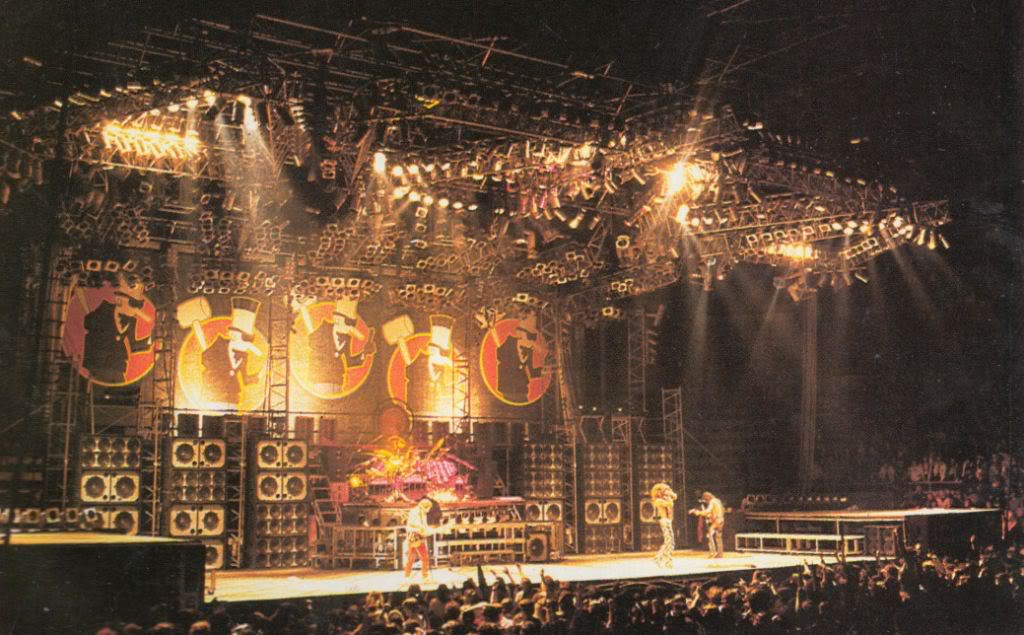
Light and Sound set up for Van Halen 1984 Live tour. Bonasera was in charge of building the power distribution and the intercom systems for many superstar bands in the 1980s. (Photo courtesy Dave Bonesera).
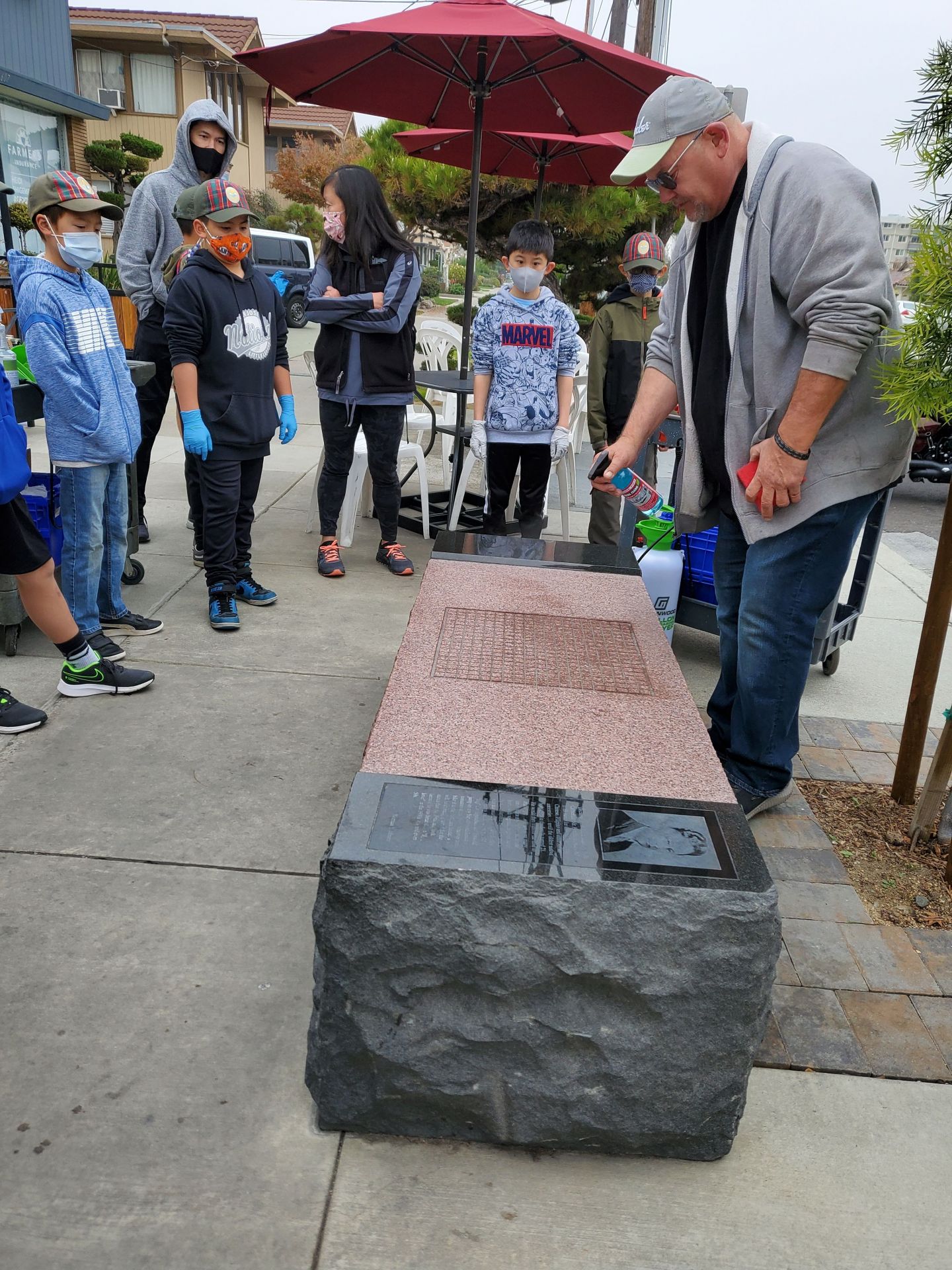
In Japantown, San Jose, CA, David Bonasera demonstrates cleaning historical granite displays to Cub Scouts and community volunteers. David: “I had three teams working with three carts on wheels. I had stocked them stocked with all of the needed cleaning solutions: MB-Stone’s Easy Oxy and Stone Pro’s Crystal Clean in a 2-quart sprayer. We used blue Doodlebug™ pads, gallons of rinse water, and lots of towels for wiping and buffing out the etched and engraved displays.”
By Peter Marcucci
Have you ever wondered what it’s like to be a rock star? I’m talking a big-time, larger-than-life superstar—surrounded with animated, top-notch musicians—banging, plucking or keying notes reverberating through an enthralled, swaying audience of thousands—who love you, marvel at you, want to meet you, party with you and get an autograph or a picture. Sounds like the most fun job in the world, right? If so, what might be the second most fun job in the world, you ask? Well ... it just might be being one of the riggers that set up the booms or the lights or the sound equipment or the instruments, and then testing the whole shebang, so when that when the band takes the stage, the show comes off without a hitch. An Odyssey Begins Attesting to all of this is Dave Bonasera. Dave began “roading” for local club bands from 1976 to 1977 to make a few bucks. Then, after high school, he began touring, he recalled. “1979 was my first U.S. tour. It was fun and exciting at the time. I worked for a company called, Show Lights. It was the largest production lighting company in the world, and we could do ten tours at a time. I ran four departments for them. My skill set was in electromechanical engineering, and I got roped into building power-distribution systems, step down transformers, communications and special effects, and when the equipment came back from the tour, it had to be maintained to keep everything up-to-snuff and ready for the next tour.” The tours would start out in Los Angeles, where the company was based, then move nationwide, and then head to Europe. Bands such as Huey Lewis and the News, The Doobie Brothers, Hall and Oates, the Rolling Stones, David Bowie, Van Halen, Don Henley, Tina Turner, and the Jacksons tour were the norm. Dave was either touring with these bands or was in the shop putting the tours together. “A lot of times I would just get the equipment ready to go, train the guys to know it, and then they would go out. Yes, I did do a lot of touring back then, and it was crazy and sometimes insane, because everything was free and there was lots of it. Sometimes, some of the guys couldn’t be on tour, because it was too much. When you’re on the outside looking in, you think, it must be great, but when you’re on the inside looking out, it was a lot of work, because you get up in the early a.m., and by 6 it’s the riggers are on the job, by 7 the lights and at 10 a.m. the sound equipment comes, and you load it all in. Then there’s the sound check, the dinner for the band, the doors open, and the show begins. You only get one shot to do it right, and can never do it wrong, because the show must go on!
"After the show, you break it all down, put it in the trucks and go to the next town. It’s the same thing every day. It’s a whole different world and not a real world, because you have all these people that love you and clap and appreciate what you’ve done, but when that’s all over with and real-life kicks in, it’s kind of a letdown, because you don’t have that appreciation until the next show. So some techs get hooked. That said, we had an incredible team that could do the concerts, the Academy Awards, the Grammys, the Emmys and the 1984 Olympics closing ceremonies in Los Angeles. A New Beginning Road- and production-weary, Dave’s last tour was with George Clinton and the Funkadelics, and in 1987 he created a cleaning business in Los Angeles. The company then moved to San Jose a few years later where it quickly morphed into doing restoration, preservation and repairs of natural stone. Currently known as the Marble Guy, Dave and his crew take on both small and large projects throughout California. Dave is also an industry educator, consultant and forensics guy that regularly diagnoses problems and specifies remedies. “Once I got out of rock ‘n’ roll, I wanted to do something different, and started my cleaning company," Bonasera continued. “From the very beginning, I wanted to use environmentally safe products and procedures to do the work, and named the company ESP, short for Environmentally Safe Products and Procedures.” About a year later, Dave met Tim from Multi Seal, who began teaching him how to refinish stone. “Tim didn’t just say, ‘Here’s polish and here’s a pad. Polish this up!’ No, he taught me about the stone itself, and what it can and can’t do, because they all react differently. I take pictures of all my jobs, and none of my guys leave here until they see the pictures, know what they’re walking into, and have all the right grouts, cleaners and sealers, because not one product is going to work on every type of stone. We have products that are made with water and products that are made with oils, and those are two different animals.” Dave employs nine very specialized technicians, and went on to say, “These days it’s hard to find the right people. Most of them have been with me for almost two decades. I supply medical, dental and vision benefits, because you want to take care of those who are taking care of you. If you don’t take care of your people, they’ll go somewhere else, and the worst thing you can do is train them to be your competitors. I don’t ever want to do that, because we are usually ahead of our competition as far as methods and technology.”
Read more in the February 2022 issue of the Slippery Rock Gazette.
▼ There's More! ▼
Notre-Dame de Miséricorde –AKA Claire’s Arch
By Sharon Koehler
Those of us who deal in natural stone (whether we supply it, sell it, buy it, fabricate it, install it, admire it or cuss it out from time to time) can for the most part can agree that natural stone is ageless and timeless. It was around before we got here, and it will be here long after we are gone. Not only do we all know it, but a man by the name of Paul Holloway knows it better than many of us. Paul Holloway is a mason and has been so for roughly 48 years. He started in the trade when he was 15 years old, in Los Angeles, and is still doing it today. He practiced his trade not only here in the United States, but across Europe. He was also a Peace Corps volunteer, designing and building schools in West Africa. Holloway owns Northeast Masonry, a successful masonry business in Mound House, Nev., that he started in 1988. Northeast Masonry holds licenses in three states. Not too many places these days can say they have been around for over 30 years. But Paul doesn’t take all the credit for his success. He realizes that he had good people, good friends, and some great inspiration along the way. Paul was working on what he called a “castle” for his family in rural Mound House, Nevada, when things took a happy turn. They added a daughter, Claire, to their family. It was that act that would eventually send Paul on a quest to create and build a masonry masterpiece on his own property
Read more in the January 2022 issue of the Slippery Rock Gazette.
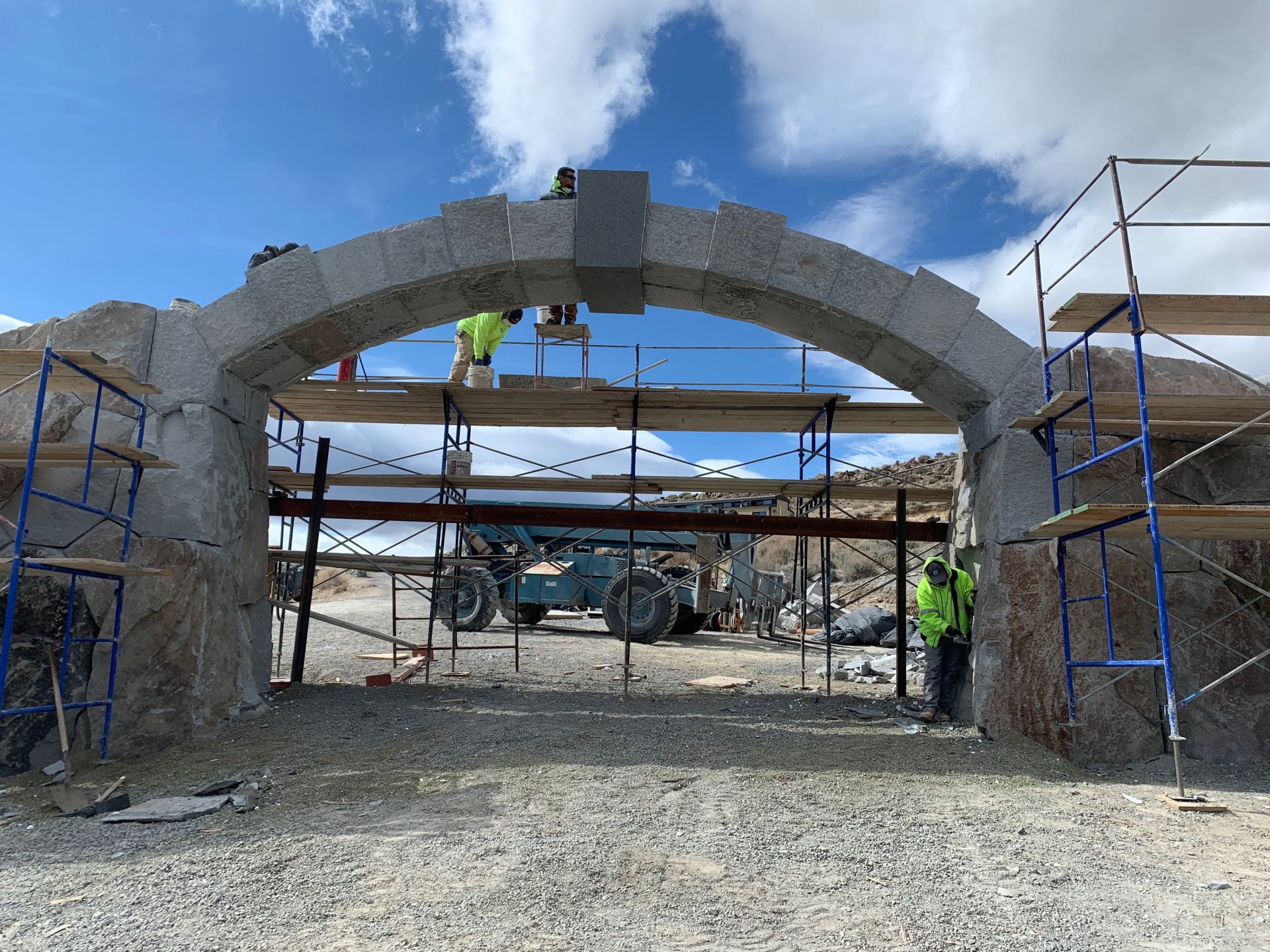
The arch was cut from black and white andesite Amacker stone locally sourced just outside of Markleeville, Calif. The piers are surface stone with patina, and cut to create a natural formation designed to fit with the terrain -- unlike the rest of the arch, which is the same stone, only without the patina. The keystone centerpiece is black granite, quarried in Raymond, Calif. This masonry-constructed arch with natural formation piers uses over 700,000 lbs. of stone, all cut with Holloway’s custom-designed wire saw.
▼ There's More! ▼
Hot Stuff- High Heat Can Damage Natural Stone
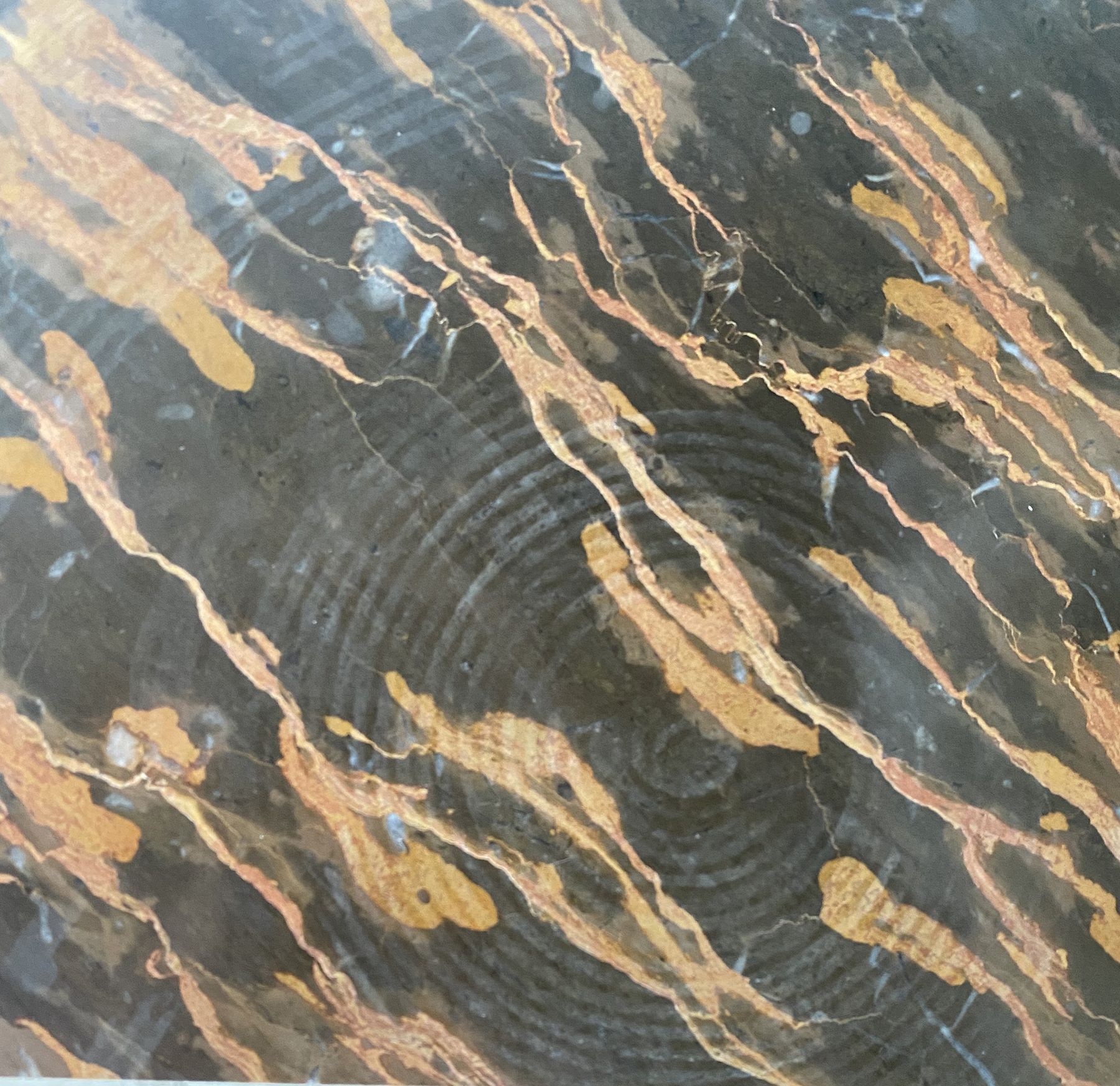
A hot pan left this crisp pattern and vivid discoloration on Portero marble.
By Karin Kirk
Many types of natural stone form in hot environments. Granite comes from molten magma that’s 1,000°F to 2,000°F, and marble is the beautiful result of limestone that is compressed and heated at a temperature of 600°F and 1,500° F. Clearly that must mean these stones can withstand heat, right? A hot casserole pan is no match for a subterranean magma chamber, after all. But unfortunately, this is one of those cases where one’s intuition turns out to be false.
Although granite starts to melt around 1,100° F, it can be damaged at temperatures much lower than that. Some stones can start to show mild effects of heat damage when exposed to temperatures around 400Ffor an hour or more. There are four ways that heat can damage even the toughest granites: The minerals can undergo physical changes, the stone can become more porous, the sealer can react to the heat, and the slab can crack. We’ll set aside the last one for another time and focus on the first three.
Check the February 2022 issue of the Slippery Rock Gazette for more!
▼ There's More! ▼
The Wrap-Up
By Rick Stimac, BB Industries President/CEO
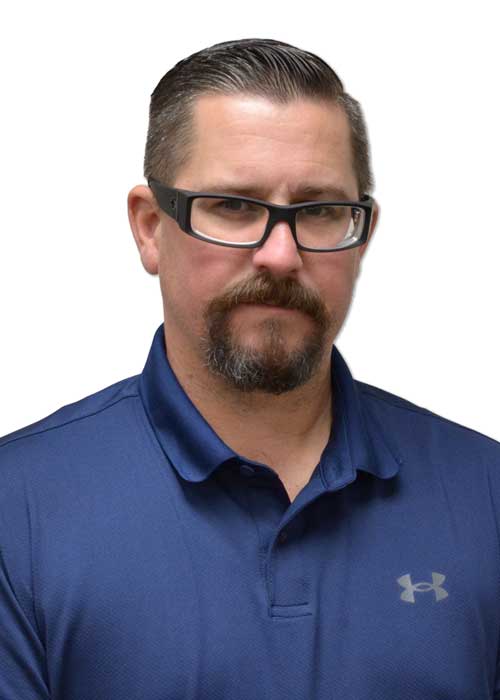
Ken Bloom
BB Industries’ (BBI) quickly growing Tech Support program expands upon its CNC support to include inline machines with the hire of stone industry veteran Ken Bloom. As we continue to grow strategically, we have realized that inline is a category that is lacking significant support, and BB Industries is filling that void for our customers. This will be a great service to fabrication shops and give us a way to share new products as well. “I am excited about the opportunity to launch this BBI Inline Division because I feel it has been overlooked by our industry," Bloom says. “I am excited about the opportunity to launch this BBI Inline Division
because I feel it has been overlooked by our industry. "Inline machines can be a challenge to operate unless the right training is provided," he adds. "That’s where I feel like I can make a difference with hands-on training, as an extension of the manufacturers. "My experience includes nearly 20 years of management, operations and fabrication, and I want to make sure that no shop is left in the dark regarding inline products." “We are not aware of any other tool vendor who is providing this level of tech services to its customers,” says Jeff Dykstra, BB Industries, VP of Sales & Marketing.
“Ken is in Southern California and will cover the U.S. for us right now. We do have plans to expand our inline service division with additional employees.” Bloom has worked with most machine manufacturers and plans to work with all who need his help with additional training for new hires, when issues arise, and also just to problem solve. On a personal note, Ken will once again work with his brother Ryan Karasz, who joined the BBI staff last year. They have been working together on and off for 12 years.
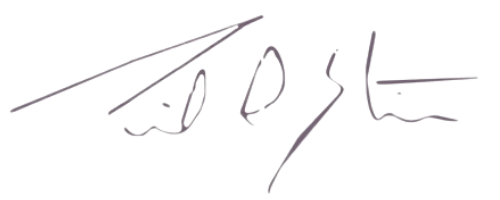

4100 Appalachian Way Knoxville, TN 37918
Hours of Operation: Monday - Friday 7:30AM - 6:00PM (Eastern Time)